Líneas de Investigación
Las líneas de investigación del Grupo están relacionadas con la innovación y mejora tecnológica en el campo de la ingeniería de superficies para aplicaciones a alta temperatura. Principalmente están orientadas a la generación de energías alternativas, así como, a la evolución de las centrales convencionales y al desarrollo de recubrimientos protectores.
A continuación se detalla cada una de ellas:
Energía termosolar de concentración
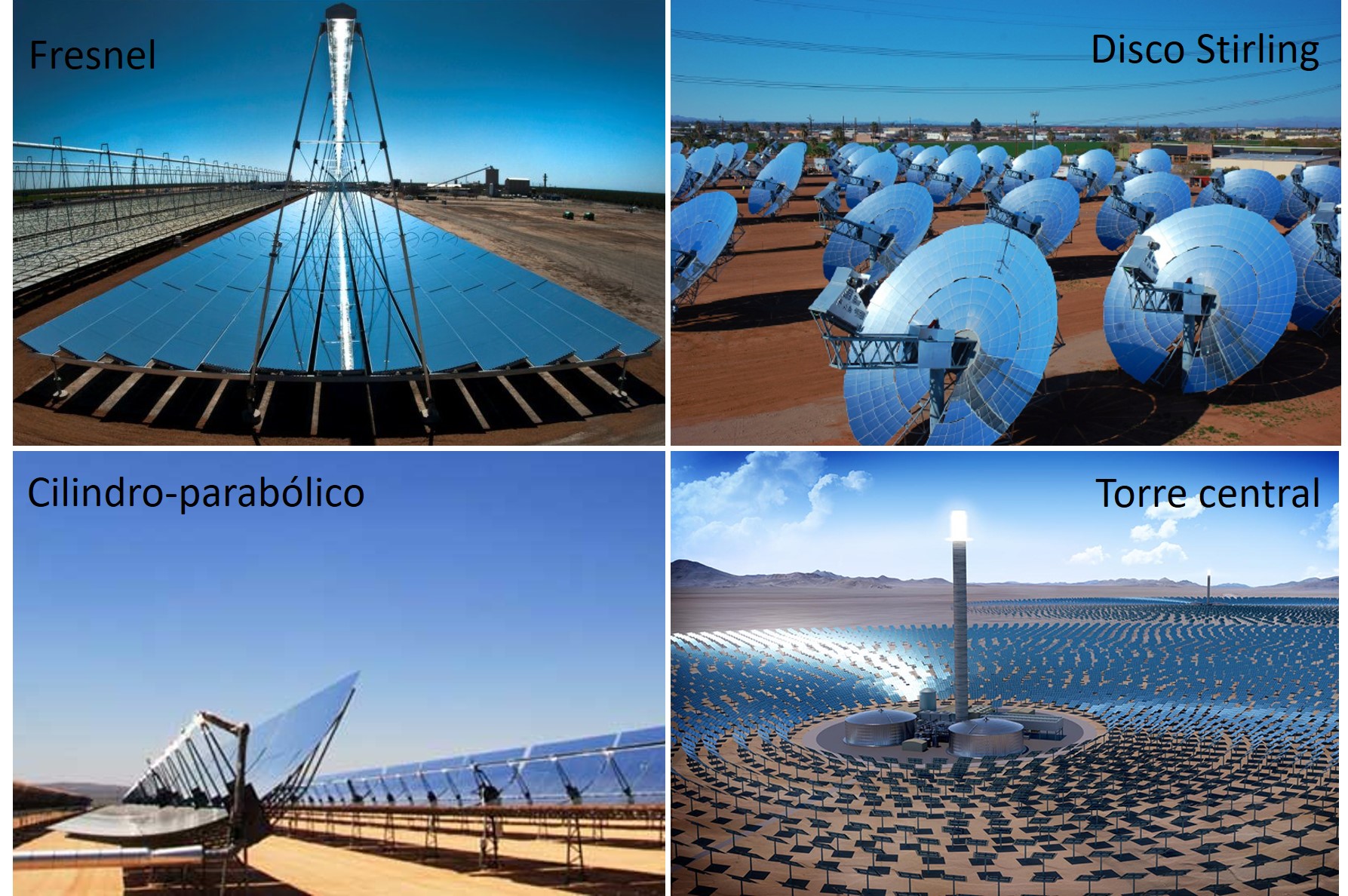
Energía basada en el vapor de agua
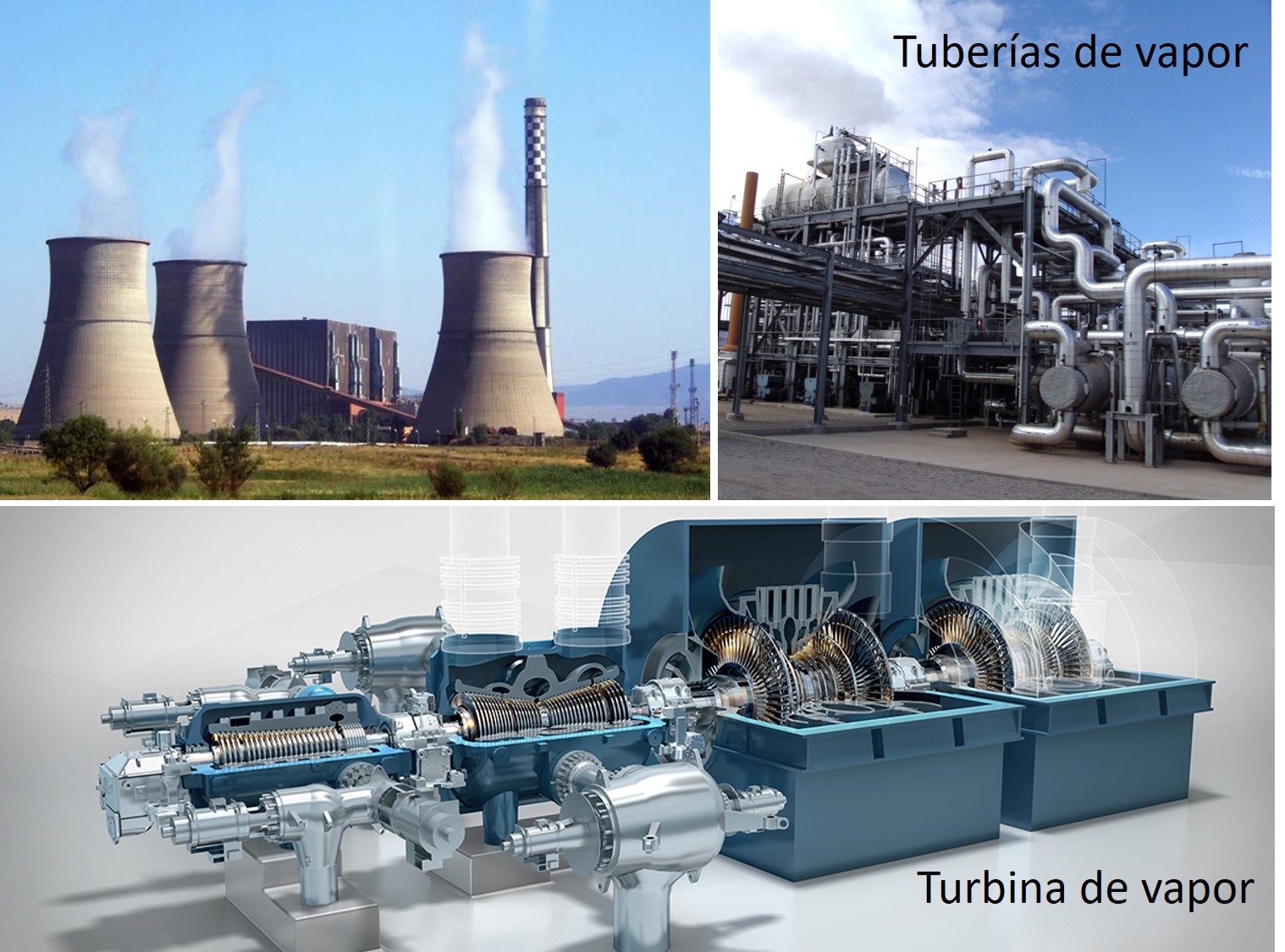
Mantenimiento predictivo y preventivo
El mantenimiento predictivo se basa en el hecho de que la mayoría de los fallos se producen lentamente y previamente, en algunos casos, arrojan indicios evidentes del futuro fallo, por lo que se apoya en un conjunto de actividades de seguimiento y diagnóstico continuo (monitorización) de un material/componente, que permiten predecir y, por tanto, prevenir el desarrollo de fallas en los materiales, de tal forma que pueda ser realizarse una intervención correctora e inmediata para reemplazar dicho material/componente antes de que suceda el fallo. Y así, poder reducir los tiempos de parada necesarios para la sustitución del componente o reparación de la zona afectada, pudiendo a su vez aumentar su tiempo de vida.
El Grupo tiene una gran experiencia en el empleo de técnicas electroquímicas para la monitorización en tiempo real de la velocidad instantánea de corrosión y para elucidar los mecanismos de corrosión. Lo que da lugar al desarrollo de sensores específicos y de sistemas de medida económicos para los diferentes medios bajo estudio. Entre ellas destacan las siguientes:
- Ruido electroquímico: mide las fluctuaciones en la señal de salida provocadas por el proceso de corrosión.
- Polarización lineal: hace pasar una corriente directa a través del metal mediante una fuente externa o potenciostato y se observa el cambio de potencial, que es registrado mediante un voltímetro y un electrodo de referencia.
- Espectroscopía de impedancia electroquímica: aplica una perturbación senoidal de potencial eléctrico de frecuencia variable al material bajo estudio y registra la respuesta en corriente dentro de una celda electroquímica.
Si las centrales de energía termosolar de concentración quieren conformar una tecnología competente se crea la necesidad de:
- Instalar un sistema de almacenamiento del calor obtenido durante las horas de sol: las sales fundidas como fluido de almacenamiento permiten operar en contínuo y como fluido de transferencia de calor permite sustituir el actual fluido (aceite térmico), con temperaturas máximas muy limitadas y con una elevada toxicidad.
- Mejorar los materiales: dado las sales fundidas causan graves fenómenos de corrosión.
- Utilizar recubrimientos con una óptica adecuada sobre los receptores de la radiación solar para que la absorción sea máxima.
El Grupo se ha volcado en el desarrollo de nuevas formulaciones que mejoren la actual (Sal Solar). Además, dada la experiencia de más de 25 años en la investigación de fenómenos de corrosión en presencia de sales fundidas, ha conformado nuevos recubrimientos que son capaces de frenar la corrosión que estos fluidos provoca.
Información adicional en la ficha de la OTRI.
Las actuales centrales basadas en el vapor de agua operan a 600-620ºC y 25-30MPa, pero se están viendo obligadas a incrementar dichas condiciones de trabajo a 650ºC e incluso 700-720ºC y 35MPa, con el fin de obtener mayor eficiencia y, en la mayoría de los casos, minimizar las emisiones de gases de efecto invernadero, así como, reducir el consumo de combustible. Por lo que los aceros ferrítico-martensíticos, empleados en las centrales actuales, han de:
- Ser sustituidos por aceros austeníticos o aleaciones base níquel, que presentan mejores propiedades fisico-químicas, pero supone un aumento considerable del coste de los sistemas por donde circula el vapor
- Modificar su superficie con recubrimientos protectores que incrementen su vida en servicio.
El Grupo trabaja en determinar los mecanismos de oxidación de materiales desnudos y recubiertos, para establecer las condiciones de operación óptimas en función de los procesos de degradación. Para ello se vale de programas de simulación computacional, de equipos que reproducen la atmósfera de vapor y de una termobalanza acoplada a un espectrómetro de masas, para determinar las fases volátiles que se puedan generar durante el proceso de oxidación.
Modificación superficial y recubrimientos protectores
Los procesos de modificación superficial con el fin último de incrementar la resistencia a la corrosión y al desgaste de los materiales en una línea principal, y de producir sistemas anti-biofouling en una segunda. Éstos se llevan a cabo a través de diversos tratamientos:
- Sin modificación química de la superficie: se incluyen mecanizado, procesos físicos de abrasión (ej: granallado) o endurecimiento por láser.
- Con modificación química de la superficie: tratamientos térmicos (ej: soplete), termoquímicos (ej: nitruración) y procesos electroquimicos (generan un oxido superficial que pasiva la superficie, como el anodizado). También se incluyen la implantación iónica y la aleación superficial por láser, así como los tratamientos con cámara de plasma. En este caso, la acción del plasma sobre el material será combinación de procesos físicos (incremento de la rugosidad por etching) y químicos (ruptura y formación de nuevos enlaces con especies reactivas). Bajo la acción de diversos gases (aire, O2) se aumenta la hidrofilia, y por tanto adherencia, de las superficies. De este modo las capas protectoras depositadas posteriormente presentarán una menor delaminación.
- Con generación de una capa superficial de composición diferente, donde se enmarcan las técnicas de deposición de recubrimientos (CVD, PVD, proyección térmica, etc), método sol-gel (ej: recubrimientos de zirconia estabilizada con ytria, YSZ; sílice modificada, etc) y los procesos de electrodeposición (ej: cromado).
El Grupo realiza estudios de simulación computacional para el diseño de recubrimientos protectores y establecimiento de composición óptima. Dichas capas se caracterizan y validan experimentalmente. También se llevan a cabo estudios de corrosión catastrófica de este tipo de recubrimientos, establecióndose como novedad los modelos de degradación, para poder evaluar su resistencia y estimar su vida remanente
Información adicional en la ficha de la OTRI.
Herramientas de trabajo empleadas
- Monitorización electroquímica:
El grado de oxidación de un material es un parámetro clave para poder predecir su tiempo de vida. En el caso de los metales, el estudio del mecanismo de corrosión se basa fundamentalmente en la cantidad de metal consumido o la cantidad de óxido formado en función del tiempo.
Debido a que las condiciones a las que están sometidos los materiales en contacto con gases, vapor o sales fundidas son cada vez más agresivas. Se crea la necesidad de monitorizar el proceso de oxidación/corrosión que está teniendo lugar.
El Grupo lleva trabajando más de 25 años en el estudio de la oxidación/corrosión en estos medios, sumado a la gran experiencia en técnicas electroquímicas, como la impedancia electroquímica (EIS), ha dado lugar al desarrollo de sensores que permiten monitorizar en tiempo real y en contínuo la velocidad instantánea y el mecanismo de corrosión. Se puede aplicar a equipos portátiles y de bajo coste.
Un ejemplo de ello es la monitorización electroquímica de la corrosión a elevada temperatura en presencia de sales fundidas, recogida en la ficha de la OTRI.
- Simulacion computacional termodinámica:
Conocer con premeditación las fases sólidas y volátiles que puedan conformarse cuando un material es expuesto a una atmósfera y a unas condiciones específicas es de gran interés, dado que da una idea inicial del carácter protector de las capas de oxidación que se pueden generar y considerar si es necesario emplear otro material o usar un recubrimiento protector con un rango composicional concreto.
Estas aproximaciones termodinámicas se efectúan teniendo en cuenta que estos cálculos computacionales son realizados en condiciones de equilibrio y a partir de amplias variedad de bases de datos de alta calidad. Por lo que hay que tener en cuenta que en corrosión a elevada temperatura se dan en muchas ocasiones procesos de reacción fuera del equilibrio.
- Simulacion computacional difusional:
También es posible predecir el efecto de la interdifusión iónica entre los elementos del recubrimiento protector y del sustrato, así como de la atmósfera a la que se encuentran expuesto. Este fenómeno de degradación da lugar a zonas empobrecidas en el elemento que ha de aportar la protección, o a la formación de fases frágiles que dan lugar a la fractura final del recubrimiento protector.
- Simulacion computacional por elementos finitos:
Se realizan estudios tanto de la distribución de tensiones en aplicaciones estructurales como de las tensiones entre recubrimiento y material base. El análisis se puede realizar sobre distintas geometrías y uniones soldadas. Suele emplearse para establecer un modelo de vida remanente con parámetros mecánicos y químicos.
High entropy alloys
El despliegue de tecnologías de captación de energía libre de carbono renovables y de bajo coste, como las plantas de concentración de energía solar (CSP), tendrá un papel fundamental para abordar las metas y objetivos propuestos en el Pacto Verde Europeo, es decir, para reducir al menos el 40% de las emisiones de gases de efecto invernadero, implementar que la obtención de energía sea al menos un 32% a partir de energías renovables y que sus eficiencias aumenten al menos un 32,5% para 2030. Para lograr estos objetivos, el rendimiento de las plantas de concentración de energía solar actuales debe ser incrementadas. Para ello, se debe aumentar la temperatura máxima de funcionamiento de las actuales y futuras plantas termo solares, ya que ello aumentará la eficiencia en la conversión térmica-almacenamiento-eléctrica.
Hoy en día, existe una apremiante necesidad por el desarrollo de nuevas aleaciones, que combinen simultáneamente superiores resistencias a la corrosión a elevadas temperaturas (RC <15 micras/año para 30 años de vida útil) con altas estabilidades mecánicas, para la fabricación de componentes clave (válvulas, intercambiadores de calor, tanques, etc) que se encuentran en contacto con fluidos altamente corrosivos a temperaturas > 600 ºC y a condiciones de trabajo cíclicas.
Con el objetivo de desarrollar nuevas aleaciones, recientemente, se han introducido conceptos que abordan el diseño de aleaciones multicomponente capaces de operar, con altos rendimientos termo-mecánicos, dentro de rangos de temperatura cada vez mayores y más elevados. Un buen ejemplo de este tipo de concepción es la idea que está detrás de las aleaciones de alta entropía (High Entropy Alloys systems, HEAs). El diseño de estas aleaciones monofásicas o bifásicas rompe con el paradigma tradicional de la metalurgia donde 2 o 3 son los elementos principales y el resto se añaden como aleantes para mejorar las propiedades resultantes de la combinación de los principales, ya que se basa en la adición de 5 o más elementos en proporciones equi o no-equiatómicas (5 ≤ cada elemento ≤ 35 at.%) donde cada elemento se considera principal para la formación de soluciones sólidas (Fig. 1). Su relevancia estriba en que cada elemento sigue comportándose de forma diferente debido a sus propiedades individuales como: el tamaño, la carga, el número de electrones, la electronegatividad, posibilitando así el desarrollo de aleaciones útiles en catálisis y en el almacenamiento de energía con propiedades mecánicas mejoradas como alta resistencia a la fluencia, dureza y resistencia, y excelente resistencia al desgaste y a la corrosión incluso a altas temperaturas (Fig. 2).
Figura 1 Figura 2
El Grupo diseña, fabrica y caracteriza HEA basados en sistemas monofásicos y bifásicos, mediante rutas pulvimetalúrgicas de elevada energía (Aleado mecánico, Fig. 3), para su aplicación en ambientes altamente corrosivos (sales fundidas, vapor de agua) y en condiciones de elevada de temperatura como posibles sustitutos de superaleciones.
Figura 3